PS1 and PS2 cabinets system
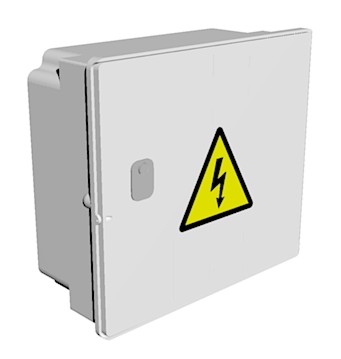
These cabinets are made as a monoblock; it is moulded at once without any other components required for assembly. Cabinets have a basic height of 272 mm (PS1) and 372 mm (PS2), a depth of 113 mm and a width of 303 mm. Individual parts are made of SMC thermosetting material, meeting inflammability requirements V0 a HB40 and adjustment for weather conditions and suitable properties for electrical engineering.
Individual components are designed to be simple to assemble and use to meet a wide range of industry-specific electrotechnical requirements. These cabinets are produced in two basic heights. Cabinets can be mounted on a pole, wall-mounted and used the in the masonry. Pole mounted cabinets are pressed with stabilizer to be mounted (stainless fastening strap or "BANDIMEX" system is used to fasten the cabinet to the pole).
Cabinet door is fitted with ribs on the outer surface. Aesthetic is not disturbed and poster sticking is difficult. Material and door construction eliminate distortion and material to bend. The door can be opened at an angle of 180 °. This is prevention before accidental damage when working inside the cabinet. Doors are sufficiently resistant to mechanical damage or destruction. Door locking is possible with locks or M5 bolt with a possibility putting the seal. Door removal is simple and can be done by pulling the door pin and taking it off after opening the switchgear.
The rear wall of the cabinet, which is primarily intended for devices installation is provided with holes for special self-tapping screws in plastic.
Assembly procedure for recessed cabinets
Cabinets are usually placed outside the building in recesses or loosely on pillars. There must be a space for operators in front of cabinet at least 800 mm depth. In case of installation near other distribution devices, safe distance must be kept. Fuse cabinets are located according to the requirements of distributors.
Cabinet door is dismantled and the dimensions of the recess are checked before mounting.
Using the wooden wedges, the cabinet is arranged to fit with the masonry surface. Raised parts should slightly protrude from the masonry. After recesses moistening, cabinet is fastened into it using cement mortar (or mounting foam). It is necessary to ensure size of cabinet before final masonry fixing, to avoid deformation (for example wooden spacer). Cabinet is then cleaned from the rest of cement mortar.
The conductor ends and cables must be insulated, alternatively fitted with terminal crimp or terminal clamps. Conductors are shaped and earthing is connected to the clamp (marked with an earthing mark). The cable entry must be sealed to prevent water getting into cabinet. This is ensured by thin layer of cement mortar.
Then the door is fitted and the door closing and locking is tested. Cabinet locks are made with a brass core and greased during production. Further greasing is no longer required.
Assembly procedure for pole mount cabinets
Pole mount cabinets are supplied with mounting stabilizers. There must be a space for operators in front of cabinet at least 800 mm depth. In case of installation near other distribution devices, safe distance must be kept. Connecting cabinets are located according to the requirements of distributors.
Stabilizers for pole mounting are attached to the rear wall of the cabinets. The UP-370 stainless fastening strap or "BANDIMEX" system is used to fasten the cabinet to the pole.
The door is removed from the cabinet and the conductors are pulled into the cabinet. The conductors are insulated and alternatively fitted with terminal crimp or "V" or "P" terminal clamps. Then conductors are marked as needed.
If the earthing outlet is fitted into the cabinet, it also must be protected by a plastic pipe to prevent mechanical damage.
The door is fitted and the door closing and locking is tested. Cabinet locks are made with a brass core and greased during production. Further greasing is no longer required.